How to reduce your manufacturing costs
Posted by Ben Mazur 12.11.2019
How to reduce manufacturing costs
- Look beyond your first order to how many parts you will order over the next 3 years
- Keep everything as simple as you can, it will have a big effect on unit costs
- Manufacturing locally can be more economical than you think
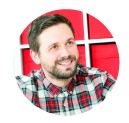
Ben Mazur
Managing Director
In this post we discuss the factors affecting manufacturing costs and some practical tips to reduce them. How much does it cost to manufacture a product? Well, that depends on a lot of things. It can vary from a few thousand pounds to many hundreds of thousands or even more. With so many materials and manufacturing process combinations there is no formula, but there are some principles which you can follow.
In order to keep this post concise we have focused on injection moulded plastic parts, assumed volumes less than 50,000 and simplified some of the explanations.
How to reduce manufacturing costs, 11 things you can do
1. Place bigger orders
A lot has to happen to manufacture a product, plastic has to be bought, tools have to be designed and machined, an operator has to set up and supervise a moulding machine, a person has to quality check, box and ship you product. These costs get spread across the number of products you are buying, if you buy more, the lower the relative costs per part will be. Placing bigger orders doesn’t exactly reduce overall cost but it will reduce your unit cost and help your profits in the long term. Placing bigger orders also puts you in a better negotiating position.
2. Talk to local manufacturers
China is still widely held as the cheapest place to get your product manufactured, and yes, there are thousands of factories there eager for your business. But consider the cost of team members going on site if you need to resolve issues or the cost of shipping delays at the border. We have seen a strong trend amongst our clients over the last 5 years moving their manufacturing operations back to the UK and benefitting from the strength of a local supply chain. Manufacturing your product closer to home is often faster and comes with lower risk, and when all of the extra costs like shipping and import duties are added up possibly a little cheaper too.
3. Simplify your parts
Complex parts have higher tooling costs (the cost for somebody to design and machine your mould tool). Complex parts also usually have longer cycle times meaning fewer parts will be made in a period of time. Complex tools with moving parts require special design and cooling, in-mould features such as metal inserts require manual insertion and twin shot parts require multiple tools and increased cycle times. Where possible keep your parts simple and they will cost less to make.
4. Tool in aluminium
Mould tools can be made from a number of different metals and alloys, usually grades of steel or aluminium. The one you use will depend on the the plastic being moulded and how long the mould tool needs to last. How long do mould tools last? Steel tools are very hard hard and can yield up to 1 million impressions or more, aluminium tools are considerably cheaper and usually yield around 50,000 impressions. Aluminium also cools more quickly than steel which can be good for reducing your cycle time. If you don’t think you will make 50,000 products before a design change, our advice is go with aluminium.
5. Keep mould finishes low key
Tool finishing is the cosmetic finish applied to the surfaces of a part. All kinds of effects can be created from mirror polish to matte to light spark, wood grain and many other textures. But mould finishes add cost and by default tool makers will often specify a bead blast finish on the tool. If you have non-cosmetic parts in your design that won’t be visible, then why not specify them as non-cosmetic and save cost on the mould finishing for those parts?
6. Reduce part thickness
Cycle time is the time it takes for the mould to close, fill with plastic, wait for the plastic to cool, the mould to open and parts to be ejected. Thicker parts take longer to cool and are more prone to cooling un-uniformly causing quality issues and greater rejections. Keep part thickness uniform and to a minimum without compromising strength and performance wherever possible. You will use less material and parts will cost less.
7. Reduce your part count
The number of parts in your product has a big impact on the cost because it has a direct affect on material amount, tooling cost and assembly times. Where possible keep your part count to a minimum and look for opportunities to combine parts where possible and where it won’t lead to added mould complexity.
8. Reduce part size
Size affects cost in two ways, it means more material and more material equals higher cost, it also means fewer products in a box, on a pallet, on a plane, on a boat, in a warehouse or on a shelf. Look at what’s driving your product size and ask yourself if it could be 10% smaller and still function effectively. Start thinking about shipping early on, design your packaging to fit the optimum number on a standard sized pallet, that way you maximise your shipping efficiency.
9. Reduce material volume
Parts with greater volume cost more and also require bigger, more powerful moulding machines which come at a premium. Thicker parts also cool more slowly, reducing cycle times. Start by looking at wall thicknesses and rib thicknesses, the optimum will vary based on the size and scale of what you are making and the material you are using.
10. Pick the right material
The material your product is made of has a direct impact on it’s cost. It also has a direct impact on performance and quality. Materials such as polystyrene are considerably cheaper but are less durable than more specialised engineering plastics such as ABS and Polycarbonate which are much tougher but come at a higher cost. This is a common tradeoff and the choice you make will depend on your industry, your market and your users’ expectations of your product and its quality. Rather than use cheaper materials and bulky design, use high performance materials, be frugal and use clever design to achieve the performance you need.
11. Make it easy to assemble
People’s time is the most costly part of manufacturing, even in countries where labour costs are low, the human element is still a major factor. So consider minimising screws, why use 6 if you can use 4? Why use screws at all if you can design everything to snap together? Design things so they can’t be put together the wrong way around, or better still design them so it doesn’t matter which way around they go. Avoid making things fiddly, build prototypes and try assembling them yourself.
Summary
There are many factors which will affect your manufacturing costs but our advice is keep things as simple as possible. Keep production nearby if you can and go and meet the manufacturers. Select appropriate materials, frugal design with high performance materials is smarter than belt and braces with low performance materials. Finally plan ahead and place bigger orders if you can.